The Comprehensive Guide to Plastic Injection Molding Companies
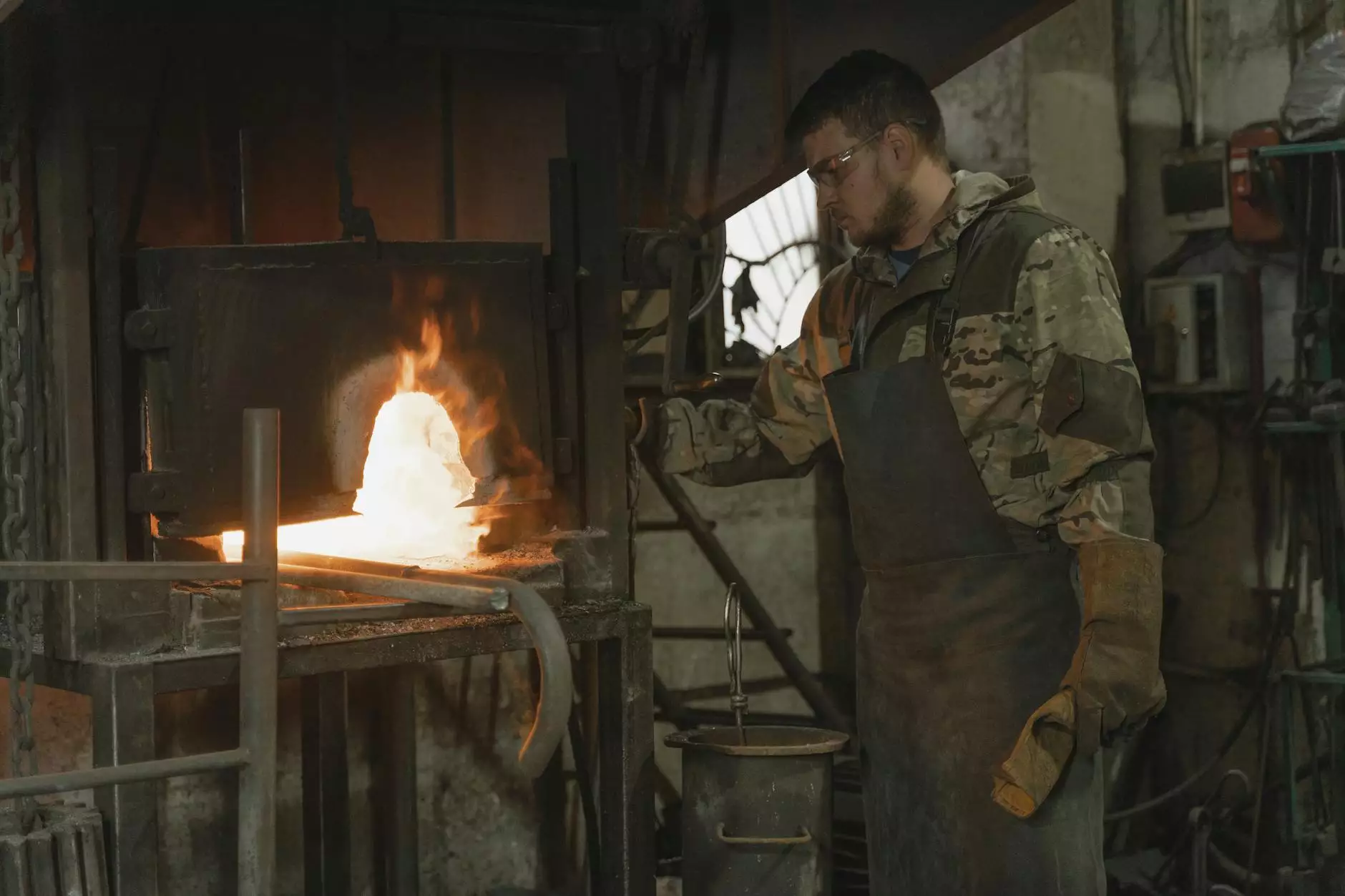
Plastic injection molding has emerged as an indispensable manufacturing process in numerous industries, enabling the mass production of intricate plastic parts. This article aims to provide an in-depth understanding of plastic injection molding companies, their processes, benefits, and how to select the best one for your business needs.
What is Plastic Injection Molding?
At its core, plastic injection molding is a manufacturing technique that involves injecting molten plastic into a pre-designed mold. Once cooled, the mold is removed, revealing the final product. This process is widely favored for its ability to produce complex shapes with high precision while ensuring efficiency and consistency.
Key Processes in Plastic Injection Molding
Understanding the processes involved in plastic injection molding is crucial for businesses considering this manufacturing method. Here are the key steps involved:
1. Design and Prototyping
The journey begins with design. Utilizing advanced computer-aided design (CAD) software, engineers create detailed blueprints of the intended product. Prototypes are often produced to validate the design before mass production.
2. Mold Creation
Once the design is confirmed, molds are constructed. The mold is typically made from steel or aluminum and is custom-designed to reflect the intricacies of the final product.
3. Injection
The raw plastic material is heated until it becomes molten. This molten plastic is then injected into the mold at high pressure. This step requires precise control to ensure that the material fills every cavity of the mold.
4. Cooling
After injection, the plastic must cool and solidify. Cooling time varies based on the material and mold design, but it is a critical phase that affects the integrity of the final product.
5. Ejection
Once cooled, the mold opens, and ejector pins push the finished product out. This step requires careful handling to avoid damaging the newly formed item.
6. Finishing Processes
After ejection, additional finishing processes may occur, such as trimming, polishing, or assembling parts to meet product specifications.
Benefits of Working with a Plastic Injection Molding Company
Choosing to partner with a reputable plastic injection molding company presents several advantages:
1. Cost Efficiency
Mass production through injection molding significantly reduces per-unit costs after the initial setup. This is particularly beneficial for businesses that require high volume production.
2. High Precision and Consistency
Injection molding allows for incredible detail and uniformity across all products, which is crucial for industries such as automotive, medical, and consumer goods.
3. Design Flexibility
Modern plastic injection molding techniques allow for intricate designs that were once challenging to achieve. This flexibility supports innovation and creativity in product design.
4. Material Options
A variety of plastics can be used in injection molding, enabling companies to select materials that best fit their application, whether it be strength, durability, or aesthetic qualities.
5. Environmentally Friendly
Many plastic injection molding manufacturers are committed to sustainability, offering options for recycled materials and fostering eco-conscious practices within their production processes.
Selecting the Right Plastic Injection Molding Company
With numerous plastic injection molding companies available, choosing the right partner can be daunting. Consider the following factors:
1. Experience and Expertise
Select a company with a proven track record in the industry. Their experience will ensure they understand the nuances of various materials and production techniques.
2. Technology and Equipment
Evaluate the technological capabilities of the company. Advanced machinery and up-to-date software can enhance production efficiency and product quality.
3. Customization Capabilities
Since many projects require bespoke solutions, it's essential to partner with a company that offers extensive customization options to meet your specific needs.
4. Quality Assurance
Inquire about their quality control processes. A reputable company should implement rigorous testing and quality assurance measures throughout the manufacturing process.
5. Customer Service
Effective communication is vital. A company that values customer service will be more responsive to your needs, ensuring a smoother collaboration.
Case Studies of Successful Plastic Injection Molding Projects
Examining real-world applications can provide insight into the capabilities of plastic injection molding companies. Here are some noteworthy case studies:
1. Automotive Industry
In the automotive sector, precise plastic components are crucial for performance and safety. A leading injection molding company collaborated with an automaker to produce lightweight and durable dashboard components, resulting in a significant reduction in vehicle weight and improved fuel efficiency.
2. Medical Devices
A prominent medical device manufacturer partnered with an injection molding specialist to create sterile, single-use syringes. The project's success hinged on the company's expertise in maintaining strict hygienic standards throughout the production process.
3. Consumer Goods
In the consumer products market, a brand sought to innovate its packaging design. By working with a plastic injection molding company, they developed a sleek, eco-friendly container that increased shelf appeal and attracted environmentally conscious consumers.
Challenges in Plastic Injection Molding
While the benefits are significant, there are challenges to be aware of:
1. High Initial Setup Costs
The creation of molds and tooling can be expensive, which might deter smaller companies or startups.
2. Complexity of Designs
Intricate designs may require specialized molds, which can complicate the manufacturing process and increase costs.
3. Material Constraints
Some materials may not be suitable for injection molding, limiting options depending on desired product characteristics.
4. Lead Times
While mass production is efficient, initial lead times for mold creation and material sourcing can be lengthy.
The Future of Plastic Injection Molding
The landscape of plastic injection molding is continuously evolving, driven by technological advancements and sustainability efforts. Companies are investing in innovative solutions such as:
1. Advanced Materials
Research into biodegradable plastics and advanced composites is paving the way for more sustainable production methods.
2. Automation and AI
Smart manufacturing processes, including AI and automation, are enhancing efficiency and precision, setting new standards for production quality.
3. Customization through 3D Printing
Integrating additive manufacturing with injection molding allows for rapid prototyping and unique design capabilities that meet modern consumer demands.
Conclusion
Plastic injection molding is a cornerstone of modern manufacturing, facilitating the creation of reliable and precise plastic parts across a wide range of industries. By partnering with a competent plastic injection molding company, businesses can leverage the benefits of this innovative process while navigating potential challenges with an experienced ally. As technology advances, the future looks bright for injection molding, promising greater efficiency, sustainability, and design possibilities.
Learn More About Plastic Injection Molding
If you're ready to explore the possibilities of plastic injection molding for your business, visit Deep Mould and discover how we can help bring your ideas to life.