Understanding the Role of Injection Molding Factories in Modern Manufacturing
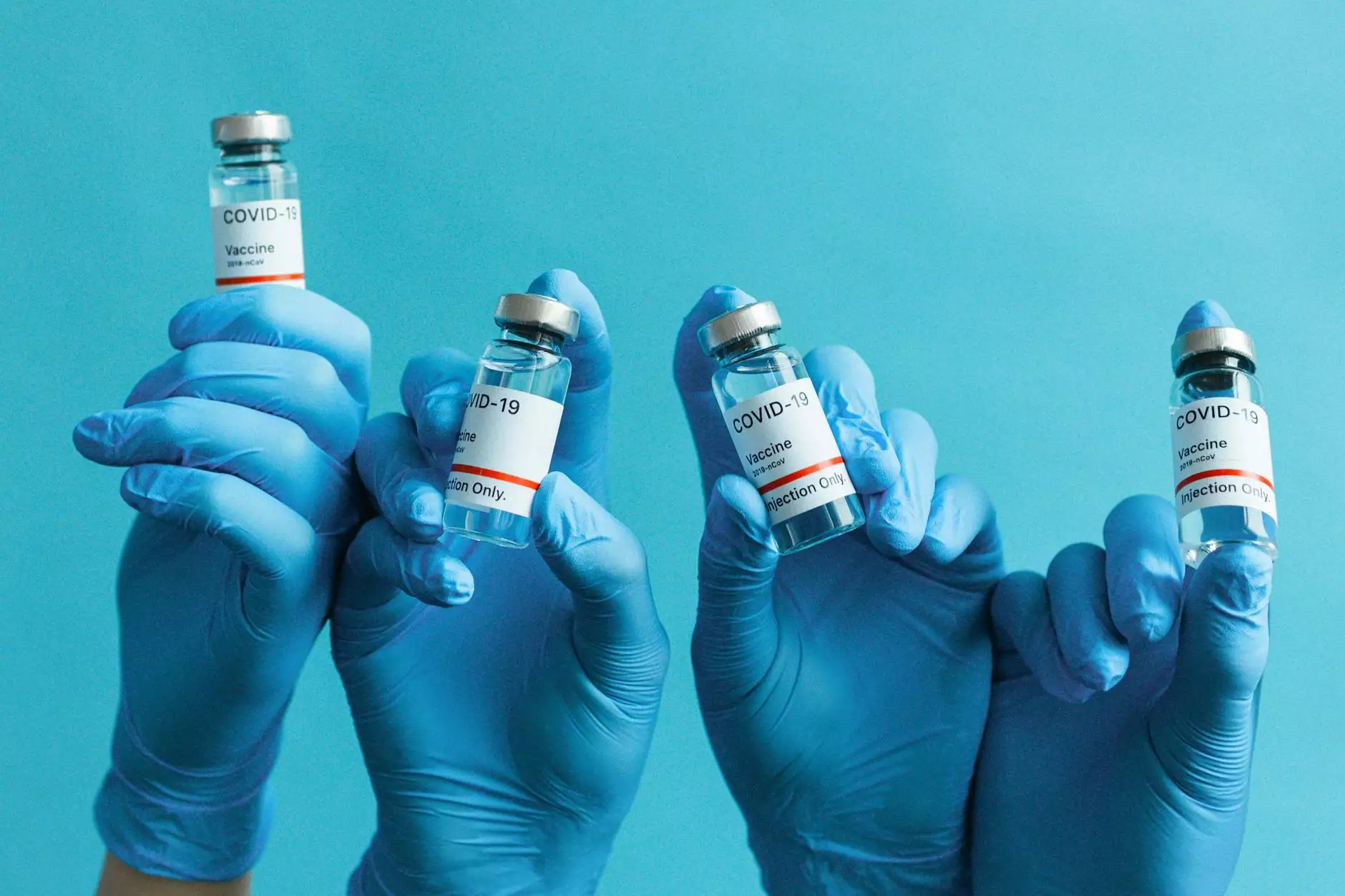
Injection molding factories play a crucial role in the manufacturing landscape, offering sophisticated solutions for producing high-quality plastic components. This article delves into the intricacies, benefits, technologies, and future prospects of injection molding, showcasing why this method is essential for businesses across various industries.
What is Injection Molding?
At its core, injection molding is a manufacturing process that involves creating parts by injecting molten material into a mold. This method is widely used for producing plastic items, ranging from simple household products to complex industrial components. The process is efficient, versatile, and allows for high precision in manufacturing.
The Process of Injection Molding
- Material Selection: The process begins with selecting the right thermoplastic or thermosetting polymer.
- Melting: The selected material is heated until it reaches a molten state.
- Injection: The molten material is injected into a metal mold under high pressure.
- Cooling: Once the mold is filled, the material is cooled to solidify into the desired shape.
- Demolding: The solid part is then ejected from the mold, completing the process.
Advantages of Using Injection Molding Factories
Utilizing the services of injection molding factories offers numerous benefits for businesses, including:
- Cost-Effectiveness: With high production rates and reduced waste, injection molding is cost-effective, particularly for large runs of identical products.
- Precision Manufacturing: Injection molding provides exceptional accuracy, enabling the production of intricate designs and fine details.
- Material Variety: A wide range of materials can be used, including various plastics and even metals, expanding design possibilities.
- Automated Production: The injection molding process can be highly automated, minimizing labor costs and increasing efficiency.
- Reduced Waste: The nature of the injection molding process allows for minimal waste production compared to traditional manufacturing methods.
Innovations in Injection Molding Technology
With the advent of new technologies, injection molding factories are evolving rapidly. Some of these innovations include:
1. Advanced Robotics
Robotic systems are increasingly being integrated into injection molding factories, improving the precision of part handling and minimizing human error. These robots handle tasks such as:
- Loading materials into machines.
- Removing finished products from molds.
- Quality inspection of parts.
2. 3D Printing and Prototyping
Many injection molding companies now use 3D printing technology for rapid prototyping. This method allows engineers to create accurate prototypes quickly, leading to:
- Faster design iterations.
- Reduced time-to-market for new products.
- Lower costs associated with traditional prototyping methods.
3. Eco-friendly Practices
As sustainability becomes a priority, many injection molding factories are adopting eco-friendly practices. This includes:
- Utilizing recycled materials in the molding process.
- Implementing energy-efficient machinery.
- Reducing water usage during production.
Applications of Injection Molding in Various Industries
The versatility of injection molding allows its application across a broad spectrum of industries, including:
1. Consumer Products
Injection molding is heavily used in manufacturing everyday consumer items, such as:
- Plastic containers and lids.
- Toys and game pieces.
- Household appliances.
2. Automotive
In the automotive industry, injection molding is employed to produce a variety of crucial components, including:
- Bumpers and dashboards.
- Light covers and interior panels.
- Fuel tanks and other under-the-hood components.
3. Medical Devices
The medical industry relies on injection molding for precision-engineered parts in devices such as:
- Syringes and IV bags.
- Implants and surgical instruments.
- Diagnostic equipment housings.
The Future of Injection Molding Factories
As the manufacturing landscape continues to change, the future for injection molding factories looks promising. Key trends shaping this future include:
1. Industry 4.0
The integration of IoT (Internet of Things) technology into manufacturing is paving the way for smarter factories. By adopting Industry 4.0 principles, injection molding operations can achieve enhanced:
- Data analytics for real-time decision-making.
- Predictive maintenance to minimize downtime.
- Supply chain optimization through interconnected systems.
2. Customization and On-Demand Manufacturing
There is a growing demand for customization in product manufacturing. Injection molding factories are adapting by offering:
- Small batch production runs.
- Personalized design services.
- On-demand capabilities to meet unique customer needs.
3. Enhanced Material Science
Developments in materials science are leading to the creation of stronger, lighter, and more durable polymers. These advancements will enable injection molding factories to produce products that are:
- More efficient in performance.
- Environmental friendly.
- Cost-effective over the lifecycle of the product.
Conclusion
In summary, injection molding factories serve as a cornerstone of modern manufacturing, facilitating advancements in efficiency, precision, and sustainability. By leveraging the latest technologies and adapting to industry trends, these factories will continue to play a transformative role in the production of consumer products, automotive components, and medical devices. Businesses seeking to compete effectively should consider the benefits of partnering with injection molding specialists to enhance their manufacturing capabilities and drive long-term success.
For more information about high-quality injection molding services, visit Deep Mould to discover how precision manufacturing can elevate your business.