Understanding Silicone Membrane for Vacuum Forming
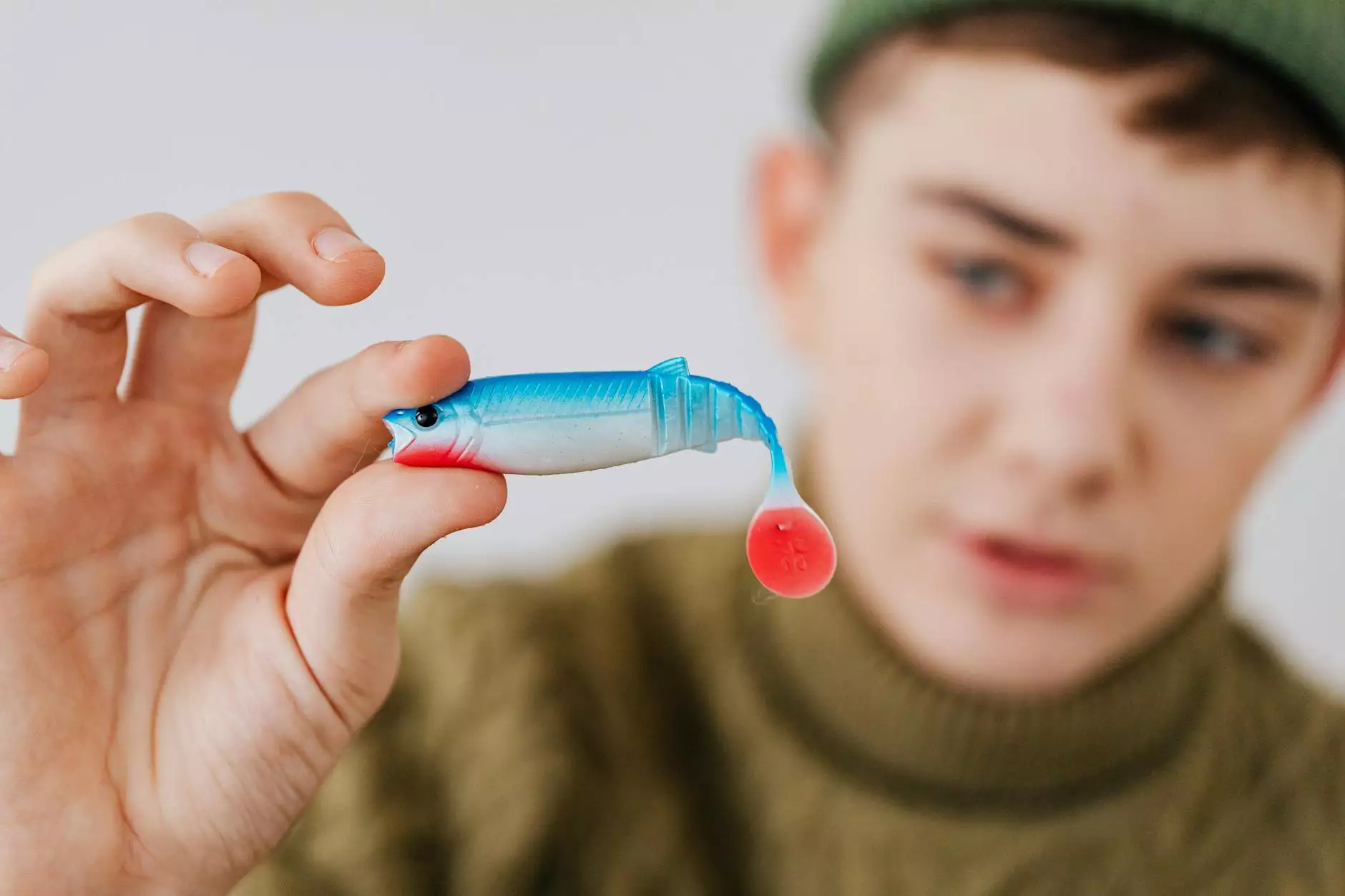
The world of manufacturing is constantly evolving, with innovative methods enhancing productivity and quality. One such advancement is the use of silicone membranes for vacuum forming, which provides unmatched efficiency and versatility in various applications. This article delves into the significance of silicone membranes, their properties, applications, and why they are a valuable addition to any vacuum forming process.
What is Vacuum Forming?
Vacuum forming is a manufacturing process that involves heating a thermoplastic sheet until it becomes pliable, and then forming it over a mold. This technique is widely used in various industries, from packaging to automotive, because it allows for the production of complex shapes with high precision. Crucial to this process is the type of membrane used, which can significantly influence the final product quality.
The Role of Membranes in Vacuum Forming
Membranes serve as a crucial intermediary between the forming material and the mold. They create a tight seal that allows the vacuum to draw the heated material into the desired shape efficiently. The choice of membrane directly impacts the effectiveness of the vacuum, the quality of the formed product, and the operational efficiency of the forming system.
Why Choose Silicone Membranes?
Silicone membranes have become a preferred choice in the vacuum forming industry due to their superior properties. Here are some reasons why silicone membranes are ideal for vacuum forming applications:
- Temperature Resistance: Silicone membranes can withstand high temperatures, making them suitable for forming thermoplastics that require significant heat.
- Durability: These membranes demonstrate excellent resistance to wear and tear, ensuring a longer lifespan and reducing replacement costs.
- Flexibility: The inherent flexibility of silicone allows it to conform to intricate mold shapes, providing accurate detail reproduction.
- Non-stick Properties: Silicone reduces the chances of the heated material sticking to the membrane, ensuring smoother product transitions and less waste.
- Chemical Resistance: Silicone membranes are resistant to various chemicals, which is crucial in environments where cleaning agents or other substances may be present.
Applications of Silicone Membranes in Vacuum Forming
Silicone membranes are employed across multiple sectors due to their versatility and efficiency. Here are some notable applications:
1. Packaging Industry
Silicone membranes are extensively utilized in the packaging industry, where they guarantee precise and consistent shapes for food containers, clamshells, and blister packs. This ensures that products are securely packaged while maintaining aesthetic appeal.
2. Automotive Sector
In the automotive sector, silicone membranes facilitate the production of complex interior components, dashboards, and instrument panels. The durability and high-temperature resistance of silicone make them ideal for this demanding application.
3. Medical Supplies
The medical industry uses silicone membranes for forming components like device housings, trays, and sterile packaging. The non-toxic nature of silicone is essential in maintaining hygiene and safety standards in medical applications.
4. Electronics Manufacturing
Silicone membranes are vital in the production of protective casings and housings for electronic devices. They ensure tight seals and can withstand the heat generated during the manufacturing process, safeguarding sensitive components.
5. Prototyping
In prototyping, silicone membranes allow designers to create models that closely mimic the final product's shapes and details. This is critical for testing and refining designs before mass production.
Benefits of Using Silicone Membranes for Vacuum Forming
Implementing silicone membranes in your vacuum forming processes comes with numerous benefits that can enhance your manufacturing operations:
- Increased Efficiency: The high thermal stability and flexibility of silicone membranes contribute to quicker cycle times, leading to faster production rates.
- Cost-Effectiveness: Although silicone membranes may have a higher upfront cost, their durability and reduced need for replacements often result in long-term savings.
- Improved Product Quality: By providing precise shapes and finishes, silicone membranes contribute to high-quality end products that meet stringent market standards.
- Versatile Compatibility: Silicone membranes can be used with a wide range of thermoplastics, making them suitable for various applications and manufacturing processes.
How to Select the Right Silicone Membrane for Your Needs
Choosing the right silicone membrane for vacuum forming requires careful consideration of several factors:
1. Thickness
The thickness of the membrane influences its strength and flexibility. Thicker membranes offer more durability but may be less flexible, affecting the quality of the formed product. Consider the specific requirements of your application when selecting thickness.
2. Temperature Range
Assess the maximum temperatures your application will expose the membrane to. Select a silicone membrane that can comfortably withstand these temperatures to prevent damage during the forming process.
3. Chemical Compatibility
Different industries use various chemicals that could interact with the membrane. Ensure the silicone membrane chosen is compatible with the substances it may encounter to avoid degradation.
4. Type of Thermoplastic
Your choice of thermoplastic will influence the type of silicone membrane required. Ensure compatibility between the two for optimal performance.
Purchasing Silicone Membranes at Vacuum-Presses.com
At vacuum-presses.com, we offer a variety of high-quality silicone membranes tailored for vacuum forming applications. Here's a guide to our offerings:
Categories of Products
Our website features several categories that can fulfill your vacuum forming needs:
- Buy Membranes: A wide selection of both silicone and rubber membranes.
- Silicone Membrane: High-performance silicone membranes designed for various industrial applications.
- Rubber Membranes: Durable rubber options for specific applications requiring different properties.
- Vacuum System Parts: Comprehensive parts necessary for assembling or maintaining your vacuum systems.
- Natural Rubber Membranes: Eco-friendly options for those who prefer sustainable materials.
Conclusion
The use of a silicone membrane for vacuum forming has revolutionized manufacturing across multiple industries due to its numerous advantages and applications. With its unmatched flexibility, temperature resistance, and durability, silicone stands out as a superior choice over other materials. By selecting the right silicone membrane for your specific needs and sourcing from reputable suppliers like vacuum-presses.com, you can significantly enhance your production efficiency, reduce costs, and maintain high product quality. Embrace the benefits of silicone membranes and take your vacuum forming processes to unprecedented heights.